Battery energy storage plays an essential role in today’s energy mix. As well as commercial and industrial applications battery energy storage enables electric grids to become more flexible and resilient. It allows grid operators to store energy generated by solar and wind at times when those resources are abundant and then discharge that energy at a later time when needed.
For anyone working within the energy storage industry, especially developers and EPCs, it is essential to have a general understanding of critical battery energy storage system components and how those components work together.
There are many different chemistries of batteries used in energy storage systems. Still, for this guide, we will focus on lithium-based systems, the most rapidly growing and widely deployed type representing over 90% of the market.
In more detail, let’s look at the critical components of a battery energy storage system (BESS).
Battery System
The battery is a crucial component within the BESS; it stores the energy ready to be dispatched when needed. The battery comprises a fixed number of lithium cells wired in series and parallel within a frame to create a module. The modules are then stacked and combined to form a battery rack. Battery racks can be connected in series or parallel to reach the required voltage and current of the battery energy storage system. These racks are the building blocks to creating a large, high-power BESS. EVESCO’s battery systems utilize UL1642 cells, UL1973 modules and UL9540A tested racks ensuring both safety and quality.
You can see the build-up of the battery from cell to rack in the picture below.
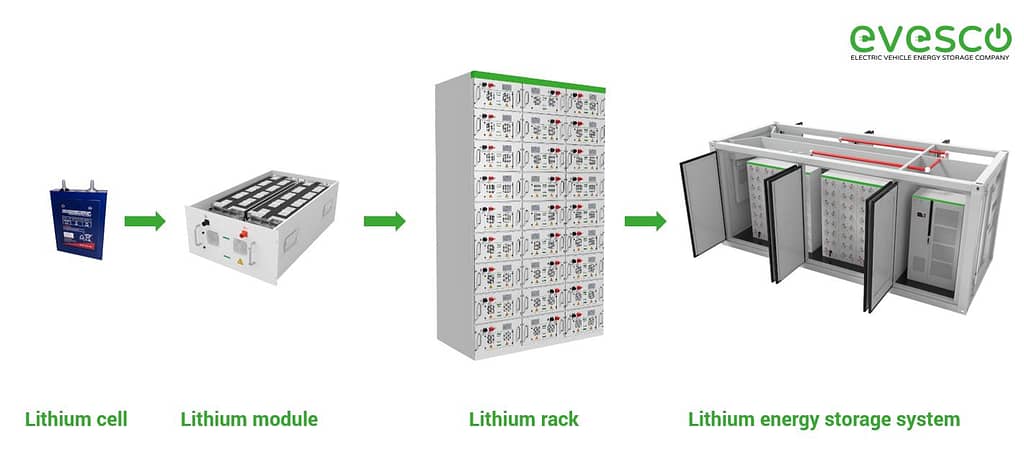
Battery Management System (BMS)
Any lithium-based energy storage system must have a Battery Management System (BMS). The BMS is the brain of the battery system, with its primary function being to safeguard and protect the battery from damage in various operational scenarios. To achieve this, the BMS has to ensure that the battery operates within pre-determined ranges for several critical parameters, including state of charge (SoC), state of health (SoH), voltage, temperature, and current. More sophisticated battery management systems, like those used by EVESCO, have a multi-tiered framework that allows real-time monitoring and protection of the battery within the BESS not just at the cell level but at the module, string, and system level. The BMS constantly monitors the status of the battery and uses application-specific algorithms to analyze the data, control the battery’s environment, and balance it. This is critical for the thermal management of the battery to help prevent thermal runaway. A well-designed BMS is a vital battery energy storage system component and ensures the safety and longevity of the battery in any lithium BESS.
The below picture shows a three-tiered battery management system. This BMS includes a first-level system main controller MBMS, a second-level battery string management module SBMS, and a third-level battery monitoring unit BMU, wherein the SBMS can mount up to 60 BMUs.
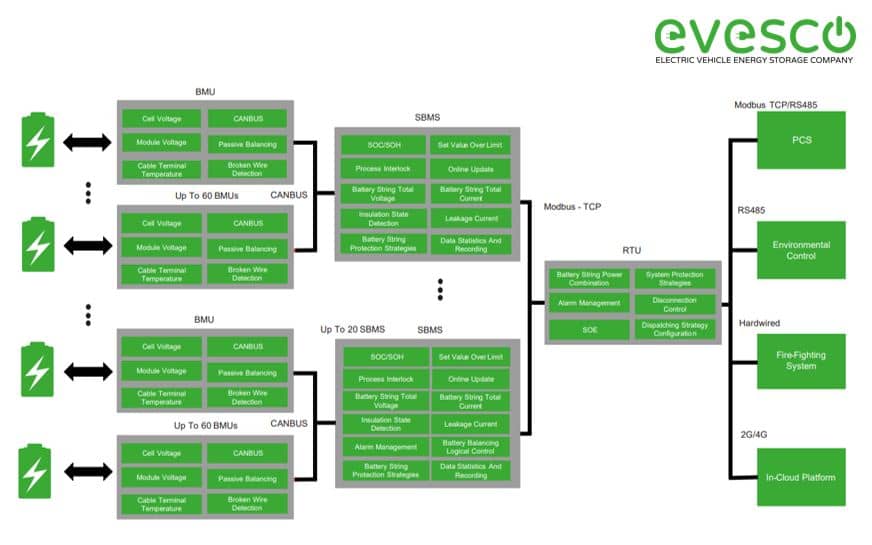
Power Conversion System (PCS) or Hybrid Inverter
The battery system within the BESS stores and delivers electricity as Direct Current (DC), while most electrical systems and loads operate on Alternating Current (AC). Due to this, a Power Conversion System (PCS) or Hybrid Inverter is needed. These devices are much more dynamic than standard inverters as they can convert power bi-directionally. This means DC power from the battery can be converted to AC power for use with grid or electrical loads, and AC power can be converted to DC power to charge the battery. This effectively gives the BESS its ability to both charge and discharge. The PCS has various modes which can be set for different charging and discharging strategies based on the specific application of the BESS. For the PCS or Hybrid Inverter to be effective within the BESS, it needs to have access to the status of the battery, so it knows when to charge and when to discharge. For instance, if you set the depth of discharge (DoD) of the battery to 90%, it needs to know when the battery is at a 10% state of charge (SoC) to stop discharging. The PCS can provide a fast and accurate power response by communicating with the battery. The PCS can be driven by a pre-set strategy, external signals (on-site meters, etc..), or an Energy Management System (EMS).
Regarding the PCS, two types of configuration are essential to know. AC-coupled and DC-coupled. For solar + storage applications, there is a choice between the two.
AC-coupled is when the BESS is connected external to the solar PV system on the AC side of the PV inverter. The BESS has its own dedicated inverter connected to the battery.

DC-coupled is when the battery is connected to the same DC bus where the solar PV lands—utilizing a hybrid inverter that is shared between the PV and the BESS.

Controller
If the BMS is the brain of the battery system, then the controller is the brain of the entire BESS. It monitors, controls, protects, communicates, and schedules the BESS’s key components, called subsystems. As well as communicating with the components of the energy storage system itself, it can also communicate with external devices such as electricity meters and transformers, ensuring the BESS is operating optimally. The controller has multiple levels of protection, including overload protection in charging and reverse power protection in discharging. The controller can integrate with third-party SCADA and EMS for complete data acquisition and energy management.

HVAC (Heating, ventilation, and air conditioning)
The HVAC is an integral part of a battery energy storage system; it regulates the internal environment by moving air between the inside and outside of the system’s enclosure. With lithium battery systems maintaining an optimal operating temperature and good air distribution helps prolong the cycle life of the battery system. Without proper thermal management, the battery cells can overheat, leading to increased degradation, malfunction, or even thermal runaway, having the correct type of HVAC system will result in better performance for the BESS and a longer life for the batteries.

Fire Suppression
The fire suppression system within a BESS is an additional layer of protection. As we mentioned earlier in the article, all BESS have a Battery Management System which ensures the battery operates within safe parameters, including the temperature. If an elevated temperature outside the set parameters is reached, the BMS will automatically shut the system down; however, in the case of a thermal runaway, the BMS cannot be relied on as the only layer of protection. That’s where the fire suppression system comes in. In the event of a thermal runaway, the fire suppression system will activate; this could be activated through gas, smoke, or heat detection, depending on which fire suppression system the BESS has. Once started, the fire suppression system will release an agent which suppresses the fire, providing a cooling effect and absorbing the heat. Several options are available for fire suppression systems, and they are usually designed according to the size of the BESS enclosure. At EVESCO, we use fire suppression systems that utilize Novec1230 or FM-200, depending on the size of the system to meet international standards.

SCADA (Supervisory Control and Data Acquisition System)
SCADA focuses on monitoring and controlling the components within the BESS; it communicates with the controller via PLC (Programmable Logic Controller). The SCADA typically communicates with the BMS to monitor battery status, and it can also communicate with the PCS/Hybrid-Inverter and auxiliary meters. From the HMI (Human Machine Interface), operators can issue start/stop commands, charging/discharging commands, and set parameters for the BMS and auxiliary systems. Most BESS can integrate with third-party SCADA systems via different interfaces, including Register Map. It is possible that SCADA can take on the role of an EMS.

Energy Management System (EMS)
The energy management system is in charge of controlling and scheduling BESS application activity. To schedule the various components on-site, the EMS communicates directly with the PCS/Hybrid Inverter and BMS, frequently considering external data points from things such as the electric grid, transformers, PV arrays, and loads. The EMS is responsible for determining when and how to discharge power, which is typically decided by the application specifics such as peak shaving, load shifting, or self-consumption. An EMS will optimize BESS performance by balancing application cycling data and battery life with the asset’s return on investment while at the same time considering the limitations of the BMS and PCS/Hybrid Inverter. The EMS will also collect and analyze BESS performance data, making reporting and forecasting easy.

These are the critical components of a battery energy storage system that make them safe, efficient, and valuable. There are several other components and parts to consider with a BESS which can differ between manufacturers. At EVESCO our BESS have rugged containerized enclosures and all 5ft, 10ft, and 20ft systems are fully assembled before shipment, a true plug-and-play solution. Discover how battery energy storage systems works in our dedicated blog.